The following report was prepared by members of the Tennessee State Architect’s Quality in Construction Committee. Contributors include the following companies: Turner, Messer, JE Dunn, Christman, Skanska, Brasfield & Gorrie, Bell Construction and TW Frierson.
Overview: Market Conditions 3Q 2023
Material Pricing and Availability, PPI
According to an analysis by the Associated General Contractors of America August update. The producer price index for new nonresidential construction—a measure of what contractors report they would charge to put up a specific set of buildings—fell 1.4 percent in July. That decrease followed no change the month prior and a slight decline in May. Association officials said contractors are finally seeing some relief from recent supply chain problems and price escalations, but the competitive market means key materials are still very hard to find.
Prices for most major construction inputs were stable or declined in July. Some of the greatest declines included diesel fuel, falling 8.4 percent for the month, steel mill products dropping 7.6 percent, and fabricated structural metal, down 6.4 percent.
Labor
Construction employment increased in 221, or 62 percent, of 358 metro areas between June 2022 and June 2023, according to an analysis by the Associated General Contractors of America of new government employment data. Association officials said the job gains in many parts of the country would have been higher if firms could find more workers to hire. The State of TN employment in the construction industry increased by 5% overall with Clarksville, TN experiencing 15% growth.
“Demand remains strong for many types of construction projects in much of the country,” said Stephen E. Sandherr, the association’s chief executive officer. “But it remains difficult for many firms to find enough workers to hire to keep pace with that strong demand.”
We can expect continued pressure on wages, as there is still a shortage of skilled workers and contractors are offering additional incentives to attract and retain workers. Electricians remain at the top of the concern list (due to industrial and data mega projects being electrical-heavy scopes).
Subcontractor availability and competitiveness continue to drive project costs. This is a result of the limited labor pool and that subcontractors remain busy. Subcontractors are forced to be more selective about the projects that they choose to pursue and in-addition they are carrying higher fees. As evidence of this, where CM/GCs typically expect a minimum of 3 bidders in every section, there are select trades where the industry is only seeing 1 or 2 bidders.
Architectural Billing Index, ABI
The Architectural Billing Index (ABI), in the South region declined December to April has now trended upward, measuring 52.3 May and 50.5 June. Greater than 50 signals increased construction activity in the future.
Miscellaneous Factors
Mega projects (industrial, EV plants and data centers) continue contributing to the electrical and mechanical equipment issues. TN Titans is seen as the next mega project that will contribute to supply chain issues.
AGC officials said that new Buy America requirements that are part of the Bipartisan
Infrastructure Law will severely limit the supply of materials contractors can use and increase the costs of those products as the guidance goes into effect. They noted that the new requirements are so strict that many products currently made in the U.S. would not be compliant due to containing small components that are sourced from abroad.
*Note: The Buy America law only applies to federal projects that are funded by the Infrastructure law.
Escalation Recommendation:
Industry recommends a 2% per quarter escalation for commercial construction projects. In addition, projects may need to take into consideration the subcontracting market and participation relative to each individual project. Industry will be in a better position towards the end of the Calendar Year to issue recommendations for future escalation forecasts.
Market Conditions Detail – 3Q 2023
Supply Chain Trends and Insights
Over the past three months, the construction supply chain has continued to improve—most notably around raw material prices for PVC resins, steel, copper and lumber—due to reduced residential demand and increased capacity as the supply chain normalizes back to pre-pandemic conditions. Roofing, structural steel, architectural interior, plumbing, electrical commodity and wood-based products all see lead times coming back to normal levels and prices stabilizing, albeit at escalated levels. Barring any disruptions, price and lead times are forecasted to remain stable in these categories over the next 6-12 months.
As reported at our last QIC meeting, HVAC and electrical gear supply chain challenges continue due to component, labor, and equipment capacity shortfalls. However, several major HVACequipment manufacturers have reported significant improvement in backlog based on
investment in new facilities, new equipment and the hiring of additional workers to increase factory capacity. With these improvements and lower raw material costs, HVAC equipment lead
times have likely peaked and will decrease for the remainder of 2023. Prices are on track to increase 10-15 percent for 2023 but may return to a more normal annual increase of 3-5 percent starting in 2024.
From an electrical equipment perspective, the electrification trend and continued data center investment we reported during our prior QIC market update will likely last for several more years.
Even though most manufacturers are investing hundreds of millions of dollars in capacity, the persistent strong demand will only moderately reduce lead times over the next 12 months.
6-12 Month Lead Time and Price Forecast
Roofing products – Roofing supply chains have fully recovered. Lead times for most items are in the 1-3 week range depending on quantities needed. Manufacturers have produced inventory and the seasonally strong roofing market should be on solid footing.
Asphalt – We anticipate pricing increases in the upcoming quarter based on infrastructure work and increases in the cost of petroleum products.
Concrete – Cement and concrete markets have stabilized and availability has greatly
improved compared to the last couple of years. However, supply challenges persist in local markets, where construction activity remains elevated. Concrete suppliers have announced a $10/cu.yd increase in concrete for January 2024 in Nashville.
Structural steel – After a slight uptick in March and April, steel input pricing has receded from the previous quarter. Fabricated Wide flange shapes have flattened in price, while hollow shapes and plate are down slightly for the year (5-8 percent).
Architectural Interiors – As a result of the cooling housing market, availability of interior products has improved and is generally within historical lead times. However, with housing starts jumping 22 percent from April to May of this year, we will closely monitor housing starts and the materials markets for any resultant changes. Additionally, the rising rolled steel costs reported last quarter have reversed course and should provide relief to pricing of metal studs. Drywall pricing has moderated and is up 2-3% YTD.
Exterior Glazing Systems – aluminum curtain wall and window wall systems are currently running 14-16 weeks lead times
Doors and Hardware – Door hardware and hollow metal door lead times continue to hold in the 7-10 week range. We continue to recommend close monitoring of electronic access control materials as some semiconductor supply issues linger.
Appliances – Appliance supply chains have improved and some distributors are even
sitting on inventory, but this varies by manufacturer and appliance type. For planning purposes, lead times should be assumed in the two to three-month range.
Elevators, Escalators. Moving Walks – Average lead times remained unchanged over the last quarter but will likely improve over the next 6-12 months as commercial projects ease. General pricing is on track to rise 3-5 percent this year as a result of material and labor cost increases. Lead times for elevators vary depending on the category and manufacturer:
• Low-rise elevators range from 14-24 weeks
• Mid-rise elevators range from 20-27 weeks
• High-rise elevators range from 40-48 weeks
• Escalators range from 12-20 weeks
Plumbing and Fixtures – Inventory continues to be healthy for most materials, allowing orders to be filled within a few days. However, lead times for certain larger diameter ductile iron pipe are still running 16-20 weeks. In the past three months, we’ve seen significantly fewer manufacturer price increases and have even noted a few select price decreases. The average sales price of PVC and copper pipe has been flat over the past 6 months. Steel pipe has steadily declined over the past three months and is down 5-7 percent compared to Q1 2023 as commodity prices and freight costs have also decreased. Over the next 12 months, fixture prices are expected to increase by 7-10 percent with an announcement likely in Q1 2024.
HVAC Equipment – While HVAC demand continues to be strong, there is evidence that lead times have already peaked, or will, in the next 3-6 months. Some categories—RTUs, AHUs, DOAS, and WSHP—are already seeing a reduction in lead times as manufacturers work through backlogs. However, chillers are the one exception as lead times are still 45-65 weeks due to continued supply chain challenges and high demand from data center projects. Price increases remain at 10-15 percent for 2023, but we believe there is a chance for more normal 3-5 percent annual increases as early as 2024.
Electrical Gear – Electrical gear lead times continued to increase over the past three
months and are not expected to decrease in the next 12 months. Even with investment in additional capacity through 2023, manufacturers have pushed out delivery commitments for some products, citing high demand and supply chain issues as primary causes.
Electrical Commodity Materials (includes lighting fixtures) – Lead times for most
commodity electrical items are down as manufacturers have stabilized their supply chains. Contractors and stocking distributors are actively reducing inventory levels as a result of high interest rates and lower demand, both current and forecasted. Lead times may temporarily increase in the future if manufacturers reduce capacity. Prices are still expected to increase 3-5 percent due to inflation of material cost and labor.
Generators – Lead times for generators of all sizes are running 45-75 weeks as
manufacturers are still experiencing high demand for all genset sizes. Long lead times are primarily due to component supply chain constraints, such as wire harnesses and semiconductor chips for controls. Data center demand shows no sign of slowing for the next few years as clients are ordering for 2025 delivery and beyond. Price increases are expected in the range of 5-10 percent in 2024.
Lab Casework and Fume Hoods – Lab casework lead times are holding steady at the standard range of 8-12 weeks. After some notable escalation in sheet steel pricing during the first quarter, pricing has fallen as underlying demand no longer supports continued escalation.
Wood Products – Lumber pricing continues to hold steady at pre-COVID levels. However, with the unexpected housing starts jumping 22 percent from April to May, we will closely monitor housing starts as they are the primary driver of lumber pricing.
Transportation – Based on slowing consumer demand and resolution of congestion at U.S. ports, shipping container activity will fully recover to “normal” levels in 2023 and container costs are now at pre-pandemic levels.
Remedies/Solutions
- Every team needs to get deeper into the supply chain. It is not enough to depend on
subcontractor and supplier input. - Contractors should be leveraging relationships with the manufacturers to access delayed materials and equipment – can push to get partial, critical orders on critical path.
- It is not enough to look at overall escalation %, you need to look closer and account for escalation material by material because of the variation between materials.
- A robust procurement strategy is essential – leads times are emphasis.
- Example item in a procurement strategy: Buying large air handlers early and designing around it.
- Cost benefit of escalation clauses – leverage allowances – talk with trade partners about allowances in lieu of trade partner taking all the risk to keep from paying worse-case scenario all the time.
- You can drive escalation into a project by buying too early.
o Understand when materials need to be on site.
o Make acquisitions just in time where possible. - Early release packages for long-lead items continues to be a good strategy…consider
warehousing strategies (costs associated with this) to ensure schedule.
THANK YOU TO OUR 2023-2024 CHAPTER SPONSORS!
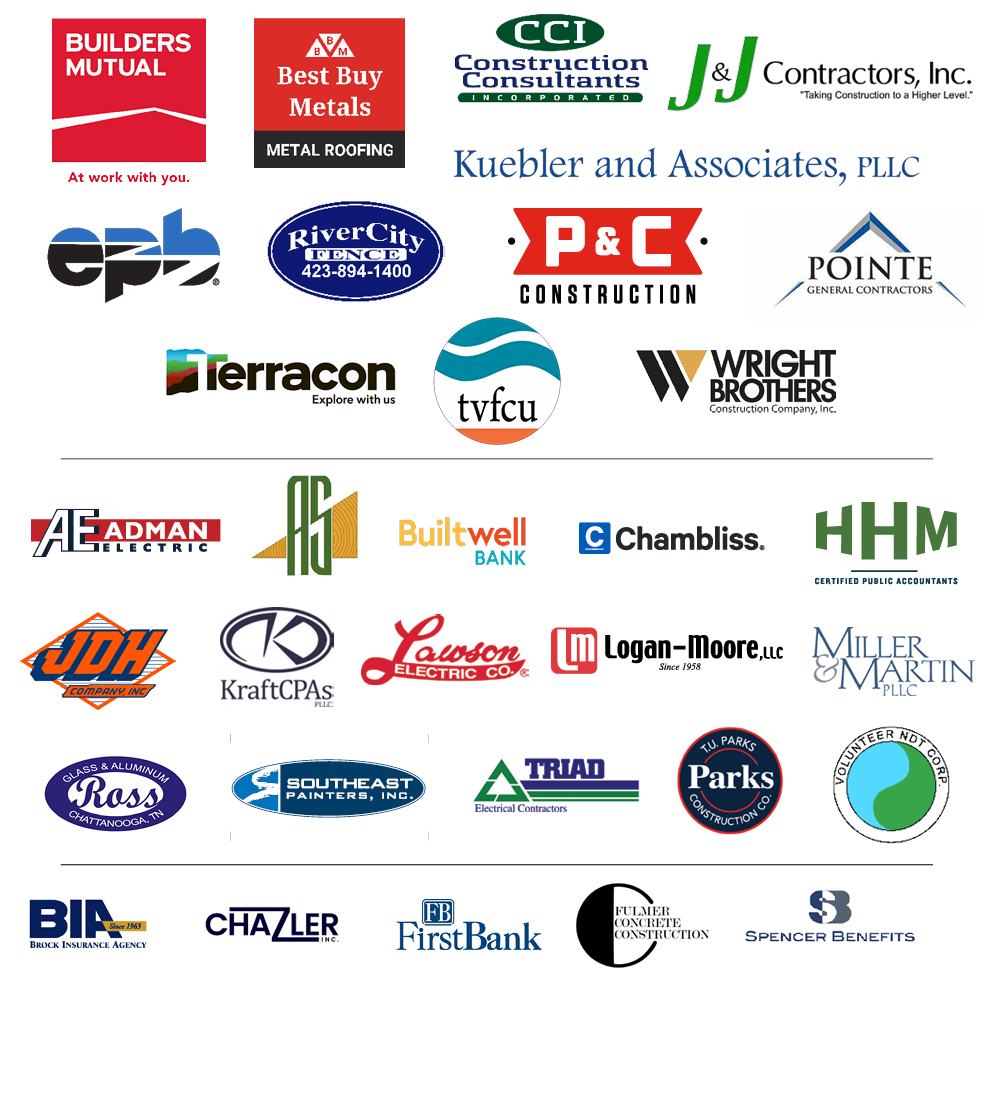